BIM Process. BIM Process Management Steps.
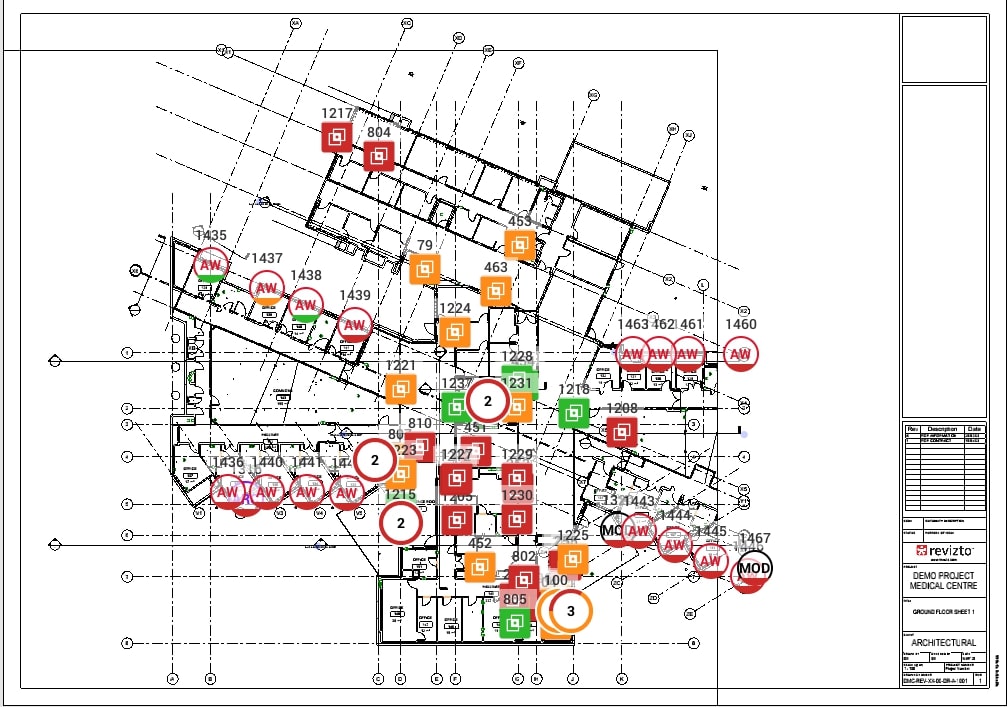
Introduction
While the popularity of BIM has been on the rise for the past twenty years, there are still many companies that do not understand the necessity of BIM in the current landscape of construction and modern technologies. BIM is crucial for design and construction teams to work together when it comes to 3D models, among other things.
The process of using BIM for different collaborative purposes within different stages of the project is a complex endeavour. It also involves a lot of resources, including both software and employees. Some examples of BIM software that is commonly used in the BIM process are Revit, Navisworks, AutoCAD, 3D Studio Max, Revizto and many others.
1. Pre-design Phase
The pre-design phase is the first step towards the realization of the project, and it usually involves several long-term decisions. One of such decisions is whether BIM should be used in the process or not. At this point, it’s extremely rare for companies not to take the many advantages that BIM has to offer, but it’s still a choice nevertheless. The only exception to this rule is the UK territory that requires BIM usage for any construction past the specific project scope. Additionally, the schematic model of the project is also created at this step, and made by the architect.
This kind of model is then presented to the project owner, with a sufficient explanation about different facilities, expected costs and the materials involved. It’s not uncommon for the owner to ask questions or offer their thoughts on the design in question, and only after going over all of the owner’s corrections can the model finally enter the design phase.
2. Design Phase
The design phase is where additional parts of BIM often start to get involved, such as scheduling and estimating (4D and 5D), and sometimes even more. We’ll go over two of those since they’re more common than the others.
Scheduling is there to assure the building created and ready within the time period that was set beforehand, and estimating is making sure that the project stays within the boundaries of the predetermined budget. The correct setup of the BIM models would significantly improve the results of these efforts.
For example, the scheduling has to keep in mind the construction process and how it works in the first place. This allows for the schedule estimates to be accurate and less prone to mistakes. Additionally, if the scheduling process is kept in mind when the BIM model is created, it would be much easier for estimating to provide more accurate numbers and predictions when it comes to budgets and materials consumed. The existence of information within different parts of the BIM model helps this process be performed correctly.
In the age of 2D drawings, it was a very laborious task to try and keep all of the possibilities and elements in mind when performing estimations. Luckily enough, BIM is capable of providing models and objects that are filled with information about their real-life counterparts, making it significantly easier to accomplish both estimating and scheduling.
Collaboration and its place in the design phase
Detailed design is where collaboration is supposed to shine the most. Performing regular coordination meetings with different participants of the project (engineers, estimators, schedulers, architects, project managers, construction managers, etc.) allows for every participant of the project to be involved in the process and provide their feedback on possible issues or setbacks.
Additionally, it’s also highly recommended to perform interference checks and clash detections on a regular basis. Some might say that this is a time-consuming process, but correcting a previously undetected error in an existing building takes way more time and resources than finding it at the design phase and fixing it before the construction even gets to that point.
The design phase is also where the BIM model could be used in several different ways, and not just its original purpose. The existence of BIM process management as a whole allows for a BIM model to be used in scheduling, elevations, walkthroughs, sections, and many other processes – potentially saving a lot of time and money within that project.
3. Construction phase
As soon as the design process is complete, it’s time to begin the construction process. Assuming that you have estimating and scheduling calculated at the design phase, you should already have a number of long-lead items purchased preemptively and that your schedule is as close to reality as possible. At this point, your work on-site should’ve already started, with people working on getting ready for the foundations to be poured, among other things.
At this stage of the construction, BIM can still be utilized in many ways to keep the process on the rails, so to speak. A specific piece of software like Navisworks can be used in the field to make sure that the intended design is followed completely, and both the construction manager and the field superintendent are collaborating with the design team for that exact purpose.
Running additional clash detection protocols is also common practice at this point to make sure that you’re not missing anything in your building as it’s being constructed. At this stage, it’s also possible to run construction simulations and predict some of the problems before they happen and disrupt the construction as a whole.
Additionally, simulations would help you make better estimations for the project as a whole, making sure that you’ll be done with the project in time. And another advantage of using BIM throughout the project’s existence is the ability to update the owner with actual walkthroughs and renderings so that they can see what they paid for.
4. Facility management
The total value of the BIM methodology spreads beyond the first three phases of project realization, making it a great addition to many facility management processes. BIM has transformed modern facility management in a lot of ways, creating a seamless bridge between digital representations of assets and their physical on-site counterparts. The new facility management framework makes it significantly easier to access detailed business data without the need to sort through large amounts of physical documentation.
The integration of BIM with facility management begins as early as the handover process, transforming construction data into operational data. The new digital handover sequence offers a complete digital twin of the existing structure for the facility manager’s tasks, including all the information available for every single building component. This level of detail dramatically improves the quality of the informed decisions facility managers can make about space utilization, renovations, maintenance, and so on.
Maintenance planning has also been changed drastically with the integration of BIM. The ability to access not only the specifications of every single building component but also maintenance history and current performance turns a BIM model into a convenient centralized tool for planning and executing any maintenance tasks. Additionally, the same BIM model can be used by technicians through mobile devices in order to receive up-to-date information about maintenance procedures, warranty details, and component information, dramatically improving service quality and response times.
Another important aspect of facility management tasks is space management, which also receives a suite of advantages from BIM integrations. The ability to access accurate and up-to-date digital representations of existing facilities makes it significantly easier for facility managers to optimize space allocation, analyze space use patterns, and plan future renovations where necessary. It is a truly priceless capability in the context of large commercial or institutional buildings, which often change their space requirements.
The BIM model itself remains a powerful tool for many daily operations, considering how many advantages it provides, from the real-time monitoring of building systems to the availability of detailed component information at any time. The sheer accuracy and versatility of the model make it possible to use a variety of predictive maintenance strategies, extending total equipment lifespan while reducing current operational costs at the same time.
Sustainability and environmental impact in BIM
Sustainability is an important cornerstone in modern construction, and BIM has been practically invaluable when it comes to creating buildings that are more environmentally friendly and sustainable. BIM can help with making informed decisions about the building’s environmental impact without losing performance, and it does so in every major phase of project realization, from early design to on-site construction.
In the design phase, engineers and architects can perform sophisticated environmental analyses using BIM as the baseline. The combination of daylighting analysis and detailed solar studies makes it possible to optimize both facade design and building orientation in order to reduce total energy consumption. Additionally, vast simulation capabilities help designers make the right choices when it comes to material selection, energy strategies, building systems, and other elements before construction itself begins.
The construction phase benefits from BIM’s accuracy and convenience, leading to a drastic reduction in waste generation and a significant optimization of total resource usage. This puts a stop to the issue of over-ordering, as well, alongside less valuable advantages, such as site logistics optimization to reduce vehicle-associated emissions or the extremely low possibility of on-site rework that wastes both resources and energy.
The operational phase might be the most important stage of the development of a building in terms of sustainability. The ability to perform sophisticated energy monitoring processes via a BIM model makes it possible to optimize a lot of existing processes. Many environmental metrics are included in this monitoring process, such as indoor air quality, water use, and everything else that may be an opportunity to improve the environmental impact of the entire structure.
Aside from day-to-day operations, BIM can also support a lot of long-term sustainability processes by improving renovation planning and maintenance workflows. The same model also assists greatly when building upgrades are needed, helping designers choose the most suitable material for each object with the least amount of environmental impact.
BIM implementation framework
A clear understanding of how BIM methodologies are implemented in an organization’s structure is just as important as knowing the benefits BIM offers to each phase of project realization. A successful BIM adoption is the product of careful planning, thorough standardization, and ongoing evaluation in order to provide as many benefits from the technology as possible.
Evaluation and assessment of prospects for implementation
The implementation process begins with pre-implementation planning. It is up to the organization to assess its current capabilities while establishing clear goals for BIM adoption and identifying its specific needs. Quite a few elements are included in this evaluation:
- Identifying potential bottlenecks
- Evaluating existing workflows
- Determining the resources necessary to complete the implementation process
- Analyzing existing hardware requirements
- Taking note of current staff capabilities
- Testing the performance of the network infrastructure
Standardization process
Standardization comes next in the process of BIM implementation. Having clear and identifiable standards for data management, model development, and collaboration protocols can dramatically reduce the complexity of integration. For example, ensuring software compatibility across platforms and choosing the specific software tools that align with the company’s requirements are both parts of the standardization process in this context. Regular evaluation of all these standards also ensures that they are up-to-date and can be adapted to the ever-changing project requirements when necessary.
Implementation plan execution
The monitoring of BIM processes is a necessity during the execution of an implementation plan to ensure that they remain aligned with established company goals. This process is responsible for tracking key performance indicators, and it also includes the identification of areas for improvement and the making of adjustments to processes or workflows when necessary. Regularly scheduled feedback sessions and team meetings assist greatly with maintaining the project’s overall alignment while addressing potential challenges that might appear during implementation.
Post-implementation maintenance
Maintenance and review are two of the last elements in the BIM implementation process. Maintenance tasks are usually taken care of by creating detailed protocols on how BIM data should be managed with sufficient accuracy and consistency, ensuring its long-term accessibility and that it is up-to-date. As for post-implementation reviews, they can be used as a means of identifying areas for improvement while also making sure that the company is still reaping every possible benefit from its BIM implementation.
Understanding the BIM project lifecycle
One of the most significant contributions of BIM to the construction industry is the ability to efficiently manage building information throughout its entire lifecycle. This comprehensive approach to data management has changed the way the construction industry works with the creation, maintenance, and use of building information throughout a facility’s entire existence.
Evolution of construction information
In a way, a BIM model can be seen as a living document of sorts, with the ability to evolve numerous times throughout the entire lifecycle of a building.
During the design phase, the model is continuously fed new information, developing from a collection of basic concepts into detailed construction documentation.
During the construction phase, the model is now updated with all the real-life information, reflecting the up-to-date conditions of every single building element on-site.
The evolution of the model continues during the operational phase, incorporating performance information, maintenance records, system modifications, and all other information generated during facility management tasks.
This evolutionary process creates a massively complex digital record of the history of an entire building. The digital nature of such records makes them far more accessible than any physical counterparts. Additionally, they can assist greatly with future decision-making processes due to the fact that every single upgrade, modification, or maintenance task is recorded alongside existing project information.
Assistance with decision-making
As mentioned before, the sheer volume of information that a single BIM model can store serves as substantial support for any building-related decisions throughout the entire lifecycle of a project. For example, facility managers can evaluate system efficiency and plan future upgrades a lot better thanks to seamless access to historical performance data. The detailed spatial and systems information in the model is a massive advantage when it comes to planning or performing renovations.
Risk assessment is another area where comprehensive building information is extremely beneficial. There are multiple advantages worth noting here:
- Change impact evaluation
- Potential conflict identification early on
- Efficient development of mitigation strategies
- Improved emergency planning
Improvements to performance tracking
Sophisticated performance tracking is also an advantage of BIM integration, with real-time monitoring capabilities offering immediate feedback on operational efficiency. Alternatively, detailed historical data also help with trend and pattern identification, making more room for improvements or issue resolution.
BIM’s approach to performance tracking goes above and beyond basic operational metrics due to the ability to include energy consumption data, space use patterns, maintenance histories, and so on. Detailed documentation of building modifications is a great benefit due to the ability to maintain accurate records for future reference, while comparing actual performance with design specifications helps with identifying opportunities for improvement.
Conclusion
In this article, we explained the BIM process and split it into several different steps (or phases). The main focus of BIM as a process is to enforce collaboration and make it easier for all of the participants of the project to work collaboratively and more efficiently.
BIM allows for a solid connection to be established between two extremely important phases of the construction – design and construction itself. As a result, the efficiency has improved drastically, and there is still room to grow.
The expansion of BIM beyond traditional design and construction purposes into facility management, sustainability, and lifecycle data modeling is the future of the construction industry. The technology also improves and evolves on a regular basis, promising better integration of BIM with many other tools and platforms in order to further enhance its value, covering the entire building lifecycle from start to finish.