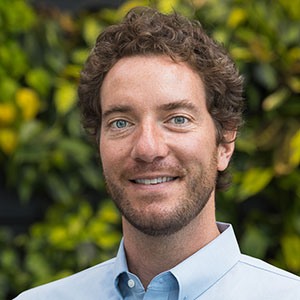
Ryan Nowosielski
Associate, Architect
It has been a life-saver from a project manager's perspective, running a large team for a complicated project. Time saved opening files for daily meetings, and quick one-off coordination questions are the most definite quantifiable returns on investment.
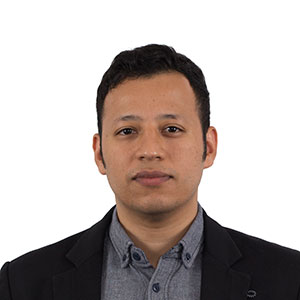
Pedro Fajardo
Designer/BIM
Revizto has reduced the amount of time spent coordinating models and moved us away from 2D documentation, allowing us to use the 3D models as deliverables.
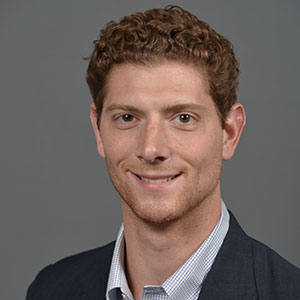
Michael Paciero
VDC Coordinator
We have fewer coordination issues, are collaborating more between architect and contractor, and leveraging the model for client review more than ever before. Revizto is a highly effective collaboration platform across all disciplines and stakeholders from the owner to the contractor to the designer.
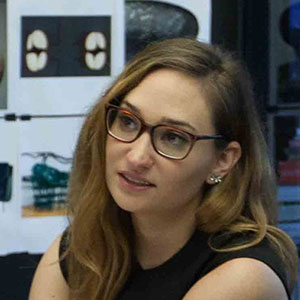
Kirsten Crock
Design Technology Coordinator
We have more rapid and thorough communication across our teams. The efficiency of categorizing/filtering and assigning issues to members is an extreme time-saver for us. Revizto gave us more accountability with records of responses and decisions, and accessible history of clash resolution and design issue decisions.
Getting the right information in the right hands at the right time has always been my biggest challenge. Revizto has been an amazing platform to build a bridge between our design and build teams and organize all of our daily, digital-information tasks in an efficient, quantifiable manner.
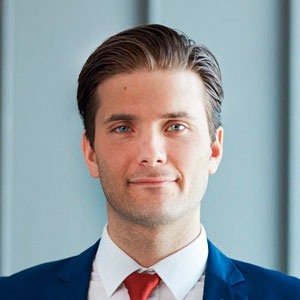
Federico Pensa
BIM-VDC Director
The ROI from using 3D collaboration instead of PDFs and emails is uncomparable. The closest example to this when we shifted from paper to digital. It's just so much better for collaboration, communication, coordination and comprehension!
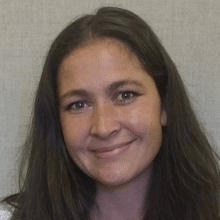
Robyn Holtgrewe
BIM Manager
The whole project team can be in-the-know at all times. We don't wait for trucks anymore or make special drives to get documents to the field; it is a one-stop-shop for all project information. No more trying to figure out which site or software houses the most current drawings or submittals - they're all in Revizto.
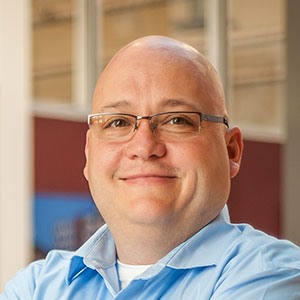
Jack Moran
Director of VDC and Integrated Services
With Revizto, issues identified in pre-con are not lost in construction, and decisions are recorded in context with associated dialogue. It gives us better visualization, leveraging both 2D and 3D data and meaningful collaboration between all stakeholders. There are significant cost benefits.
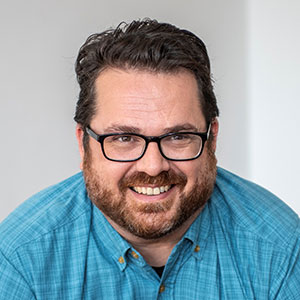
Jonathan Marsh
CEO \ Construction Technologist
I would point to a drastic reduction in the total number and length of coordination meetings, and the elimination of almost all onsite coordination meetings. I estimate time-savings around 80 hours for two weeks, per coordinator, for a near 3 million dollar mechanical job.
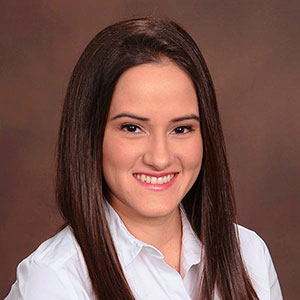
Paulina Acosta
VDC Manager
We have reduced man-hours of VDC personnel from training on the platform, maintaining viewpoints, updating drawings, and not having to be present in every coordination meeting. The content is available for project teams to consume and do their issue tracking without much help from VDC.
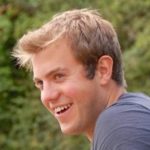
Mike Ford
Digital / BIM Manager
It's a single federated space for 2D, 3D and data, moving BIM into one portal. It allows for the model to be validated at handover by physical site checking. As a feedback loop, we can capture building changes on very small projects, and changes can be marked up in the field.
Revizto has changed how our Project Leaders and Designers look at a project. We update the progress daily and entire team have a good sense of the project's status. It's satisfying to see the tag "Solved" or "Closed" and be able to see that from over 1000 issues, big and small; you resolved 95% of them.
Revizto+ brings more functionality into an already powerful platform. The inclusion of clash automation brings efficiency to this process and enables clash resolution to be integrated into a single coordination workflow. Most impressive is the forward-thinking approach to bring a data-driven process, enabling true automation of the process all within a single platform.

Kyle Forlong
Digital Engineering Manager
There is a direct reduction in cost by elimination of software and time savings through consistency of information flow and data integrity. Transparency in clash identification, management of supply chain process to ensure their coordination is targeted and effective.

John Simpson
Head of Digital Construction
Revizto+ is single place to run clash detection and create issues while reducing syncing time and minimizing the multiple handling of information.

Belal Faquiri
VDC Coordinator
Revizto+ has drastically saved me a ton of time on clash detection. Using its fluid tools, it has helped find clashes I couldn't locate through a manual review. Revizto+ interface and tagging has made it easier to create presets to present during my meeting.
Our ROI is in the few man-hours, prevented reworks, clashes identified, quicker coordination meetings, and dollars in any regards to the previous or elimination of other software.
The time allotted for running clash tests and producing reports can be completed in half the time it normally takes using previous outdated software. Creating group sets, grouping clashes, and condensing clash reports into a precise issue tracking format helps that.

Patrick Fingleton
Digital Design Coordinator
With Revizto+, I think 20-30% in time savings would be a conservative estimate, especially when compared to our current clash detection processes.

Michal Wojtak
Director of Integrated Construction
Clash Automation helps to minimize amount of time spent flying through the model trying to identify Issues.